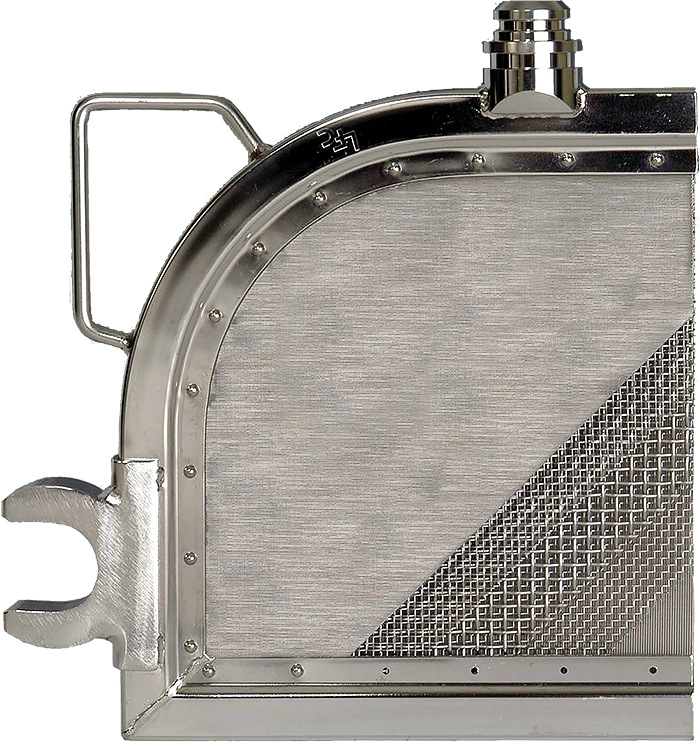
Vertical Pressure Leaf Filter Systems
Vertical pressure leaf filter systems
Amafilter® vertical pressure leaf filter systems are engineered to deliver exceptional filtration performance across a wide range of industrial applications. Their unique design allows for a large filtration surface area, thanks to the optimized shape of the filter leaf elements, ensuring high flow rates and efficient solid-liquid separation.
These systems consistently achieve high filtrate clarity, especially after the clarification cycle, making them ideal for use in processes where product purity is critical. Additionally, a variety of filter aids — such as diatomaceous earth, perlite, or cellulose — can be integrated to enhance filtration efficiency and further improve the quality of the filtrate.
BENEFITS
• Proven technology.
• Fully automated, ensures safety.
• Small footprint required, maximized space.
• Easy access to the filter leaves for removal of the cake
• Full automation means limited maintenance and lower operational costs.
• A closed filtration system for complete safety when in use.
• Short regeneration time between filtration cycles, reducing operating costs as the filter can filtrate for longer periods without disruptions.
• Easy to clean pressure filter leaves.
• No rotating parts, keeping maintenance to minimum.
• Reinforced pressure filter leaves provide extended lifetime.
• Specifically designed self sealing cover gaskets for a perfect sealing solution and maximum safety.
Vertical pressure filter leaf system for dry and wet cake discharge
Vertical Pressure Leaf Filter Systems with Dry Cake Discharge – Efficient Solid Recovery and Product Purity
Amafilter® vertical pressure leaf filter systems with dry cake discharge are ideal for applications that require efficient solid-liquid separation and minimal product loss. Common uses include the filtration of sugar, cocoa butter, and edible oils, as well as processes like activated carbon removal, molten sulphur filtration, and catalyst recovery in chemical industries.
These systems are engineered to maximize yield and reduce residual product content in the filter cake—in some cases, by up to 20%, depending on the application. When the filter cake is the desired end product, high-purity cake production can be achieved through filter cake washing, ensuring optimal quality for downstream processes.
For efficient discharge, the dried filter cake is released via a pneumatic vibrator and butterfly valve located at the bottom of the vessel. This design ensures fast and clean discharge, reducing downtime and improving operational efficiency.
The drying phase is typically performed using compressed air, inert gas, or steam, depending on the specific process and product requirements.
Products
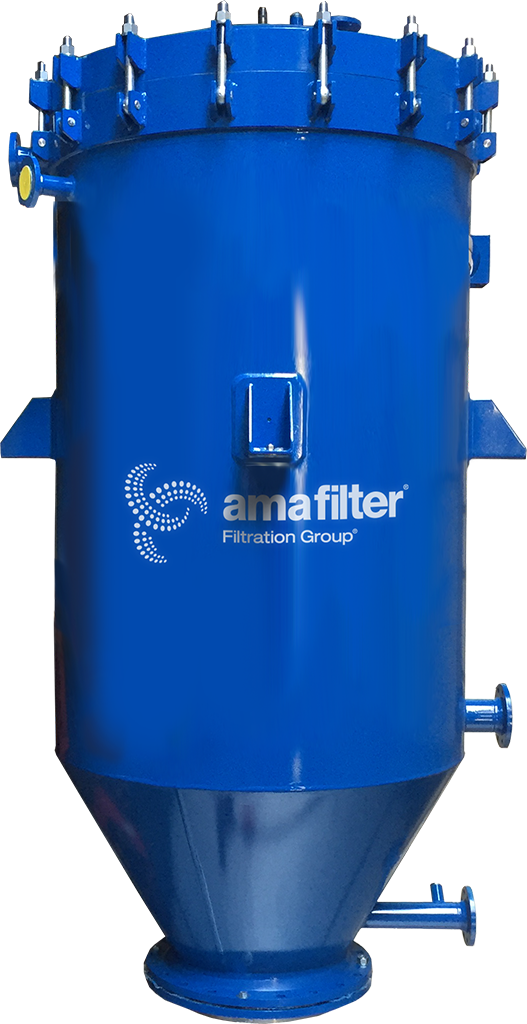
Versis®
Vertical Pressure Leaf Filters
The Versis® is a fully automated system with double sided stainless steel pressure filter leaves. It is suitable for most applications.
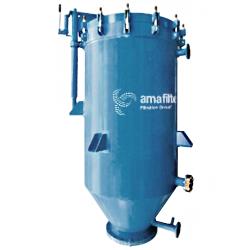
MVDCD
Vertical pressure leaf filter
The MVDCD vertical pressure leaf filter system requires only a small footprint and provides easy access to the pressure filter leaves for removal of the cake.
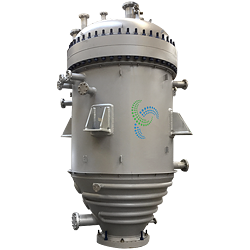
MVWDCD
Vertical pressure leaf filter
This system filters catalyst particles. It filters with an 88 m2 filtration area and is designed to feature a half pipe heating jacket for controlling the temperature of its contents.
Services
We take our responsibility in partnering with our customers seriously and provide a range of services aimed at supporting our customers effectively and assisting them to resolve their filtration challenges.
Contact us
Find out more about how amafilter®, part of Filtration Group, can assist you solve your solid liquid filtration challenges and improve your processes.