
Chemical Applications
Biofuels
Biofuels are renewable, biodegradable alternatives to fossil fuels and play a critical role in the global energy transition. They are derived from a variety of biological feedstocks including used cooking oil (UCO), animal fats, non-edible vegetable oils, agricultural residues, and other organic materials. Biofuels are used in transportation, power generation, and industrial heating, offering a sustainable way to reduce greenhouse gas emissions.
Amafilter® designs advanced filtration solutions that support the production of high-quality biofuels across the globe. We work closely with our customers to engineer systems tailored to their specific feedstocks, plant designs, and performance requirements.
Benefits of using Amafilter® equipment in biofuel production
Filtration is essential in biofuel processing to ensure the removal of solids, impurities, and contaminants that can negatively affect downstream equipment, catalysts, and final fuel quality. Amafilter®’s solutions deliver efficient, reliable, and cost-effective filtration that helps biofuel producers:
- Reduce energy consumption across the plant
- Minimise maintenance and downtime
- Improve process efficiency and throughput
- Lower operational and lifecycle costs
- Achieve consistent, high-purity biofuel output
- Prevent blockages and reduce feedstock losses
- Ensure clean feedstock for critical downstream units like hydrotreaters
- Meet strict international fuel quality standards (e.g. EN, ASTM)
We recommend our Cricketfilter®, the Versis® vertical pressure leaf filter systems together with our Bag Filters and Jonell Systems® High Flow equipment to ensure the final product meets the required international standards.
Acids and Alkalis
Amafilter®’s filtration solutions effectively separate and remove contaminated solid liquid and are ideal for use in chemical applications.
Acids and alkalis are aggressive chemicals and as such require specific filtration solutions and equipment to ensure an effective filtration process.
Due to the strong nature of these chemicals, it is essentials that the equipment and materials used in these processes can endure the attack of extremes of pH during the complete filtration cycle.
Amafilter® have extensive experience in providing filtration solutions that will ensure you are maximising your productivity, meeting your plants operational goals whilst ensuring you deliver a quality product in the safest possible way.
We recommend our Cricketfilter® system for acids and alkalis applications and our team of experts work closely with our customers to ensure the right product specifications are used to meet your specific process requirements.
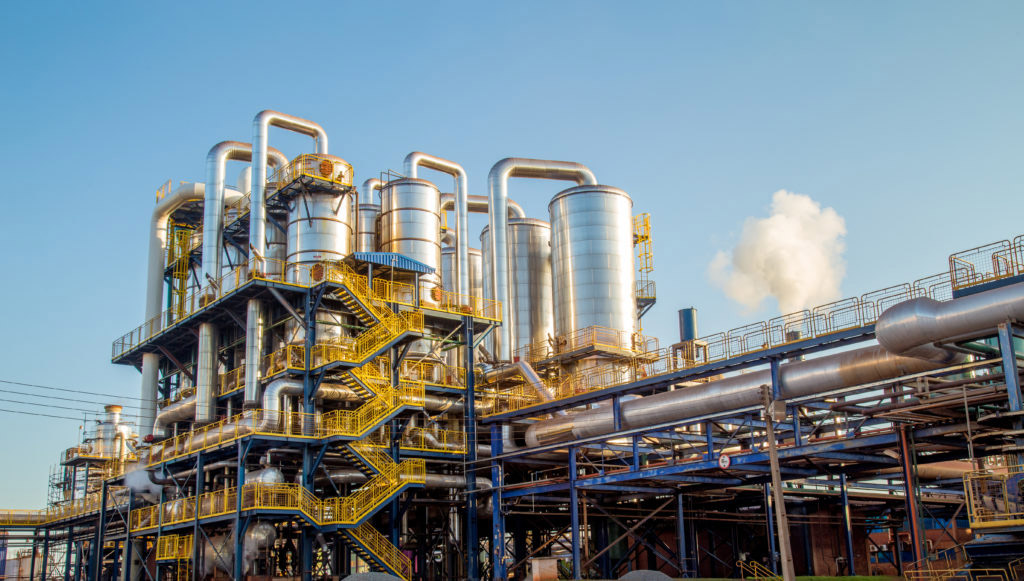
Catalyst Recovery
Catalyst recovery systems are used to recover particles of catalyst, including platinum, palladium, rhodium, rhenium and rhodenium left over from the filtration of edible oils, used cooking oils (UCO) and recycled animal fats.
During filtration, catalyst deposits form on the outer surface of the filter element, resulting in an increase in pressure drop. Once the system senses the pressure drop, cleaning of the filter elements begins through drain valves and back purging mechanisms.
When the cleaning cycle is complete, the catalyst particles are collected and removed through a bottom drain valve, allowing the next filtration cycle to begin. And, depending on the system, nitrogen, compressed air, solvents, steam or gas may be used during the back purging process. Amafilter® offers filtration solutions to assist with catalyst recovery. Find out more about our Cricketfilter® system which is ideally suited for this application and will assit delivering efficient extraction of impurities and unwanted substances from the filtration process.
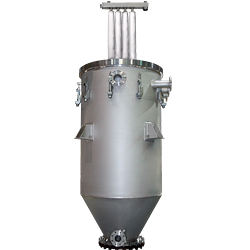
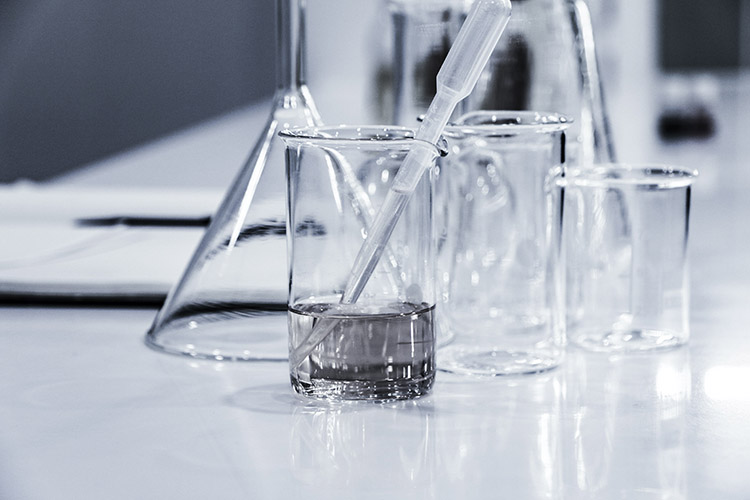
Chemical intermediates
Amafilter®’s filtration systems effectively separate and remove contaminated solid liquid and are ideal for use in Food & Beverages, chemical and mining & mineral applications.
An efficient filtration process is essential to remove liquid contaminants as they cause a variety of issues including:
- Damage to the foul contactor and filter leaves
- System corrosion
- Increase in the cost of wastewater treatment
The separation of liquid and liquid contaminants can be a complicated process, depending on the properties and specific viscosity, gravity and interfacial tension of the two liquids.
Large chemical plants, like fertiliser and hydrogen peroxide plants, require several chemical intermediate processing steps to remove common and uncommon contaminants from reaching the final product and affecting its quality. Amafilter® offers filtration solutions to assist with chemical intermediates. We recommend our Cricketfilter® or the Versis® vertical pressure leaf filter system as both deliver efficient extraction of impurities and unwanted substances from the filtration process.
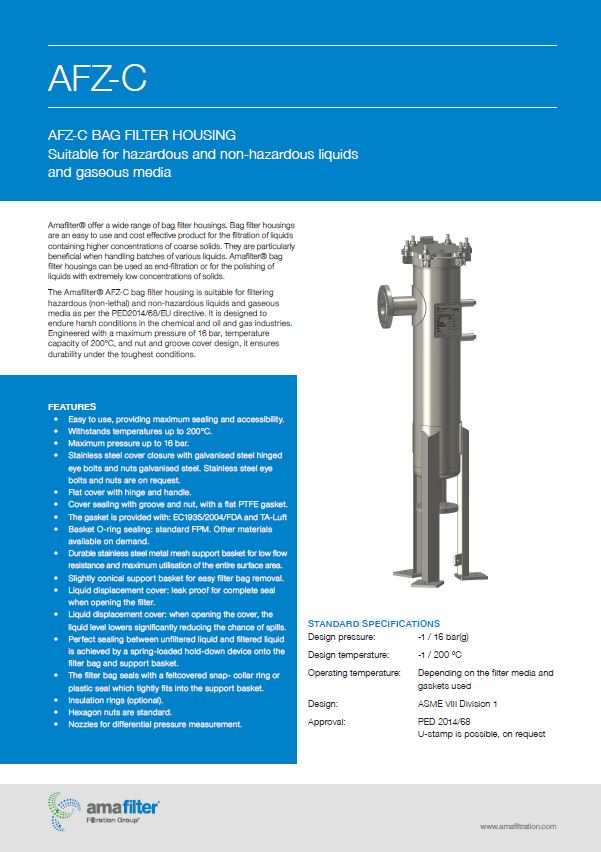
The Amafilter® AFZ-C single bag filter housing is:
Specifically designed and developed to deliver optimal performance under the most challenging chemical applications.
Suitable to filtrate hazardous (non-lethal) and non-hazardous liquids
Suitable for gaseous media
Designed to meet heavy duty applications where high pressure and high temperatures are required, generally outside the norm.
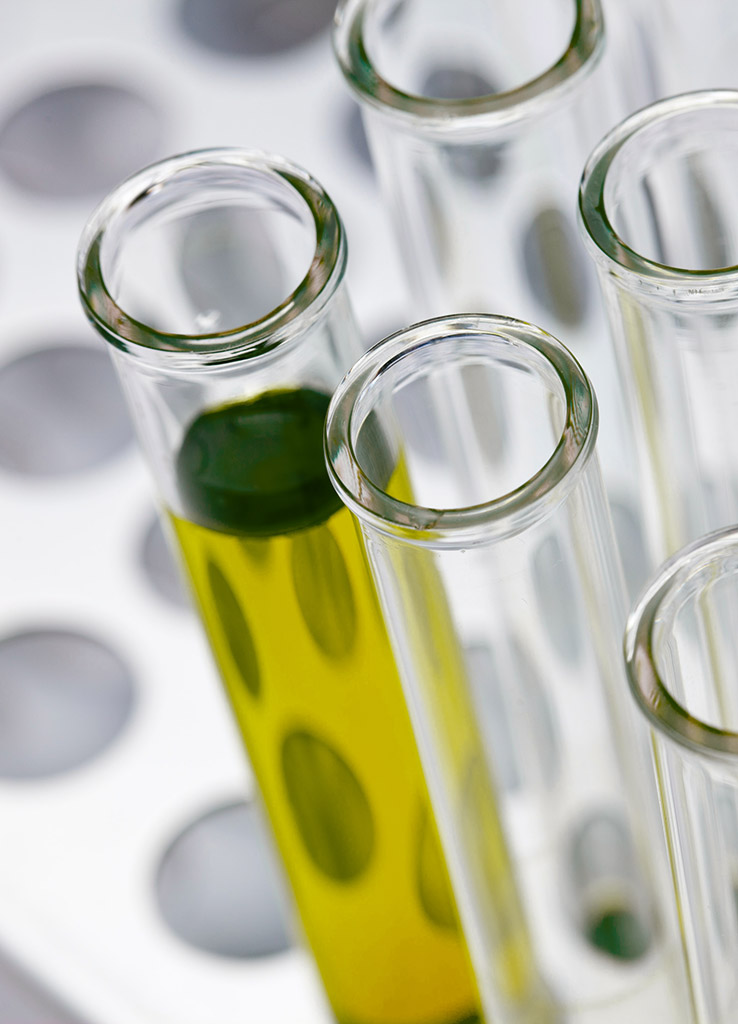
Oleochemicals
Oleochemicals derived from edible oils, used cooking oils (UCO) and recycled animal fats contain solids, soaps, glycerol and trace metals. The finished product requires the efficient removal of the unwanted substances through a combination of process knowledge and filtration solutions which include specific hardware and consumables.
Amafilter® offers filtration solutions to address solid liquid filtration, with specific expertise gained in the Oleochemical sector. We recommend our Cricketfilter®, the Versis® vertical and horizontal pressure leaf filter systems to deliver efficient extraction of impurities and unwanted substances for this process.
Paraffin Wax
Paraffin wax is a white or colourless soft solid that consists of a mixture of hydrocarbon molecules containing between twenty and forty carbon atoms. Paraffin wax is solid when at room temperature and begins melting at temperatures above around 37 °C (99 °F). It’s boiling point is >370 °C (698 °F). Common applications for paraffin wax include lubrication, electrical insulation, and candles; dyed paraffin wax can be made into crayons.
Paraffin wax was first developed in Germany during 1830 and marked a major advancement in candlemaking technology, as it burned more cleanly and reliably than animal fat candles and was cheaper to produce.
The amafilter® range of Versis® vertical pressure leaf filter has been designed for use in paraffin wax filtration process
The Versis® MVWDCD-2000/1500/88 vertical pressure leaf systems are manufactured in carbon steel and are suitable for the filtration of catalyst particles from a paraffin wax stream.
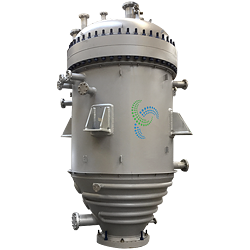
Resins
Amafilter®’s filtration solutions effectively separate and remove undissolved, used solids from liquid and are ideal for use in chemical applications.
There are two types of resins: natural resins and synthetic resins. Natural resins derive from tree secretions and these can only be dissolved in organic solvents such as turpentine oil.
In today’s industrial markets, synthetic resins are mainly being used. Synthetic resins are used as a reactive intermediate for the production of thermosetting plastics and are components in paints and adhesives. Synthetic resins can be modified by the addition of vegetable oil, animal oils or natural resins.
Producers of resins are continuously looking to increase operational efficiencies, improve product quality and deliver more competitive end product to the market.
Amafilter® have extensive experience in providing filtration solutions that will ensure you are maximising your productivity, meeting your plants operational goals whilst ensuring you deliver a quality product in the safest possible way.
We recommend our Cricketfilter® system for resin applications and work closely with customers to find the correct specification to meet their filtration processes and deliver efficient extraction of impurities and maximising yield in a safe, healthy and productive manner.
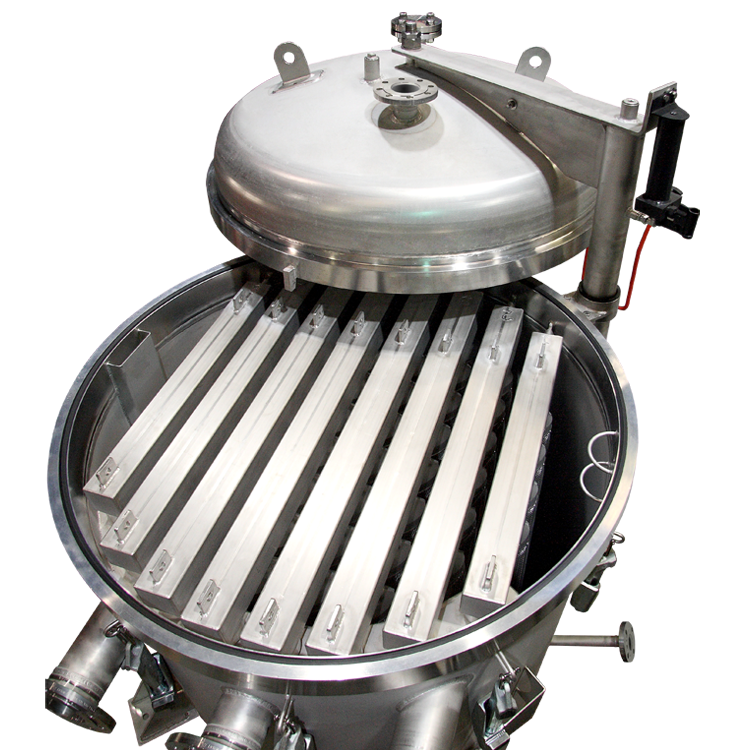
Services
We take our responsibility in partnering with our customers seriously and provide a range of services aimed at supporting our customers effectively and assisting them to resolve their filtration challenges.
Contact us
Find out more about how amafilter®, part of Filtration Group, can assist you solve your solid liquid filtration challenges and improve your processes.